- Sound waves will not travel though paint
- Remove any rust
- The spatter will impede the contact of the probe and the parent material surface
- Spatter will reflect the back will echo signal and give spurious indications
Eurotech an authorized Agent of American Welding Society(AWS). We conduct AWS CWI Examination with documented training in INDIA and MIDDLE EAST. For More Information contact to Mr.Puneet Sharma E-mail: (aws.cwi.training@gmail.com)
Monday 20 February 2017
Q:- Why is it essential to clean the surrounding parent metal adjacent to the weld metal made by MMA(SMAW)which is to be ultrasonically tested?
Sunday 12 February 2017
Q:- While inspecting a weld on a 100mm thick high carbon steel plate with tolerance of +5mm you find the weld is visual acceptable, however the parent material has several arc strikes present adjusted the weld approximately 3mm drop deep, what course of action would you take?
1. None I am only inspecting the weld
2. Recommended that the area be dressed smooth
3. Recommended that the area be dressed smooth followed by MPI
4. High carbon steel is net susceptible to cracking so I would weld over the arc strikes then blend them
2. Recommended that the area be dressed smooth
3. Recommended that the area be dressed smooth followed by MPI
4. High carbon steel is net susceptible to cracking so I would weld over the arc strikes then blend them
Sunday 5 February 2017
Q:- When reviewing a radiograph of a weld made by the MAG(GSMAW)process, you notice a very bright white inclusion in the weld, which of the following best describes this indication?
1. Tungsten inclusion
2. Spatter on the cap
3. Copper inclusion
4. It is most likely to be a film mark
2. Spatter on the cap
3. Copper inclusion
4. It is most likely to be a film mark
Monday 30 January 2017
Q:- Charpy impact tests showing a flat but rough surface after the completed test, this would indicate which type of failure?
1. Fatigue
2. Ductile
3. Fatigue to ductile
4. Brittle
2. Ductile
3. Fatigue to ductile
4. Brittle
Monday 23 January 2017
Q:-What is a typical ARC voltage setting when welding with the TIG (GTAW) process?
A. 18-20V
B. 24-26V
C. 10-12V
D. 70-90V
C. 10-12V
D. 70-90V
Friday 13 January 2017
Friday 6 January 2017
Monday 2 January 2017
Thursday 29 December 2016
Q:- If the welder who performs this procedure qualification test is also qualified, in what position that individual qualified for production welding?
a. F,OH groove in plate
b. F,H,OH fillet in plate
c. F fillet in pipe
d. None of the above
e. All of the above
b. F,H,OH fillet in plate
c. F fillet in pipe
d. None of the above
e. All of the above
Friday 16 December 2016
Q:- What is the required electrode classification for this qualification?
A. E70XX
B. ER70S-X
C. E6XT-X
D. A and B
B. ER70S-X
C. E6XT-X
D. A and B
Tuesday 13 December 2016
Q:- Hot pass Temperature?
- Equal to work peace temperature
- More then work peace temperature
- Less then work peace temperature
Tuesday 6 December 2016
AWS CWI Seminar and Exam
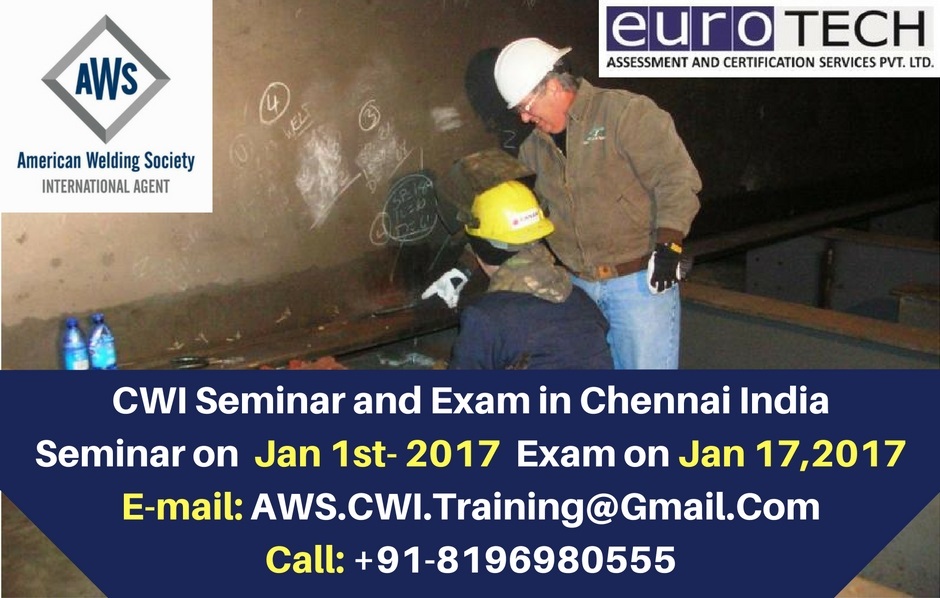
American Welding Society Certified Welding Inspector AWS CWI Course Chennai
This class is designed for inspectors and engineers working in petrochemical or fabrication facilities. The course prepares the student for the AWS-CWI (Certified Welding Inspector) exam. This is an
Intensive one-week course with a heavy emphasis on the technical and inspection aspects of welding. This course content includes:
We “EUROTECH” introduce ourselves as a multinational training & certification company.
Eurotech is an authorized agent for AWS American Welding Society for its certification program like AWS-CWI/SCWI/CAWI and more...
We conduct AWS Examination with documented training in Chennai India regularly.
Who Should Attend CWI Certified Welding Inspector Course?
All personnel whose responsibilities are in making decision, exercising of judgment concerning welding operations in the following industries. Like Oil and Gas, Manufacturing, Petrochemical, Power Generation and Power Stations, Ship Building/Ship Repair and Construction, Offshore Fabrication, Railways, Service and Maintenance and Metal Fabrication.
Eligibility CWI Certified Welding Inspector Exam/Seminar:
Minimum of 5 year industry experience or Minimum of 3 year industry experience with degree/diploma holders in engineering, technology, engineering physics or physical science
- Associate or higher degree in engineering technology, engineering, or a physical science 3 years
- High school diploma plus two or more years engineering/technical school courses 3 years
- High school diploma plus one year engineering/technical school courses or one or more years of vocational education and training in a welding curriculum 4 years
- High school diploma or approved high school equivalency diploma 5 years
- At least 8th grade 9 years
- Less than 8th grade 12 years
Course Type:
6 Day Authorized Seminar
CWI Course Benefits:
- Official Course for AWS CWI Certification
- 6 Days Intensive Training
- Includes Basic NDT Techniques and Welding Techniques
- Results in Deeper Understanding of Welding Quality
CWI Exam Pattern:
Part A – Fundamentals 150 2 hours 72% Close Book
Part B – Practical 46 2 hours 72% Close Book
Part C – Code Book 60 2 hours 72% Open Book
CWI Course Description:
Welding Inspection Technology Workshop - 3 DAYS
Helps prepare you for the CWI/CWE Exam (Part A) The Welding Inspection Technology Workshop is packed with information on nondestructive examination methods applicable to common welding processes. It will assist welding inspectors and welding educators with knowledge of welding and inspection fundamentals useful on the jobsite. In addition, this seminar will prepare examination candidates for Part A (Fundamentals) of the CWI examination.
Visual Inspection Workshop ( 1.5 Day)
Helps prepare you for the CWI/CWE Exam (Part B) This workshop provides hands-on training in the use of weld measurement tools and plastic weld replicas to determine the sizes of various weld discontinuities. Students will compare what they find to the criteria in a sample codebook to determine the acceptability or rejection criteria of the sample weldments. The workshop also includes a sample practical examination to prepare test candidates for Part B (Practical Applications) of the CWI examination. By attending this workshop, you can learn: Use of inspection tools. How to ensure compliance with the applicable code. Dos and don’ts of documentation. When a discontinuity is acceptable. When a discontinuity can be rejected. Why visual inspection can be the most effective NDE technique.
API 1104 Code Clinic ( 1.5 DAY)
Helps prepare you for the CWI Exam (Part C) if you are testing to API 1104 This four-hour course covers general provisions of API 1104, including qualification of welding procedures for welds containing filler-metal additions, design and preparation of the joint for production welding, nondestructive testing and acceptance standards, and automatic welding with and without filler-metal additions. Candidates will be given the Course material for training before the workshop and are supposed to come with a thorough reading in the class.
Click here to Check Our Next AWS CWI Seminar
Click Here to Take free AWS CWI Exam
How to Renewal your AWS CWI Certificate?
If you want to renew your CWI Certificate? Contact us for the renewals of your AWS-CWI, SCWI certifications well before 8-weeks of expiration.
Renewals process for CWI Certified Welding Inspector:
The renewal process is part of your continued certification according to QC1:2007.The validity of the certification is 3 years and Certified Welding Inspectors can renew their status by applying in the prescribed application format before the expiration date of the certification.
If the renewals are not applied before expiration, the candidates lose their CWI Certified Welding Inspector status and will have to reappear for fresh certification.
Please Contact To Puneet Sharma via phone: +91-8196980555 or by email at aws.cwi.training@gmail.com to reserve your place early and to be issued a CWI application.
If you have any questions, please feel free to ask!
If you want to Attend AWS CWI Seminar, Please fill out the Enquiry Form and Get More Details:
Full NameE-mail:
Your Details:
Tuesday 29 November 2016
Questions related to Pipe Fittings: -
1. How can flanges be classified based on Pipe Attachment?
Answer: -
Flanges can be classified based on pipe attachment as: -
Slip – on. : - The Slip-on type flanges are attached by welding inside as well as outside. These flanges are of forged construction.
Socket Weld. : - The Socket Weld flanges are welded on one side only. These are used for small bore lines only.
Screwed. : - The Screwed-on flanges are used on pipelines where welding cannot be carried out.
Lap Joint. : - The Lap Joint flanges are used with stub ends. The stub ends are welded with pipes & flanges are kept loose over the same.
Welding Neck. : - The Welding neck flanges are attached by butt welding to the pipe. These are used mainly for critical services where the weld joints need radiographic inspection.
Blind. : - The Blind flanges are used to close the ends which need to be reopened.
Reducing. : - The reducing flanges are used to connect between larger and smaller sizes without using a reducer. In case of reducing flanges, the thickness of flange should be that of the higher diameter.
Integral. : - Integral flanges are those, which are cast along with the piping
component or equipment.
2. How can flanges be classified based on Pressure- temperature ratings?
Answer: -
Flanges are classified based on pressure temperature ratings as: -
#A. 150
#B. 300
#C. 400
#D. 600
#E. 900
#F. 1500
#G. 2500
Pressure temperature rating carts in the standard ASME16.5 specify the non-shock working
gauge pressure to which the flange can be subjected to at a particular temperature.
3. How can flanges be classified based on facing?
Answer: -
Flanges are classified based on facing as: -
- Flat face. (FF)
- Raised face. (R/F)
- Tongue and groove. (T/G)
- Male and female. (M/F)
- Ring type joint. (RTJ)
4. How can flanges be classified based on face finish?
Answer: -
Flanges are classified based on face finish as: -
- Smooth finish.
- Serrated finish.
5. Where the smooth finish flange & serrated finish flange finds its use?
Answer: -
The smooth finish flange is provided when metallic gasket is provided and serrated finish flange is provided when non-metallic gasket is provided.
6. What are the types of serrated finish provided on flange face?
Answer: -
- Concentric or
- Spiral (Phonographic)
7. How the serration on flanges is specified?
Answer:
The serration on flanges is specified by the number, which is the Arithmetic Average Rough
Height (AARH).
8. Where the concentric serration is insisted for face finish?
Answer: -
Concentric serration are insisted for face finish where the fluid being carried has very low
density and can find leakage path through cavity.
9. How the Gaskets are classified based on the type of construction?
Answer: -
Based on the type of construction, gaskets are classified as: -
- Full face.
- Spiral wound metallic.
- Ring type.
- Metal jacketed.
- Inside bolt circle.
10. What is the most commonly used material for Gasket?
Answer: -
Compressed Asbestos Fibre.
11. Which type of gasket is recommended for high temperature & high-pressure application?
Answer: -
Spiral Wound Metallic Gasket.
11. What are the criteria for selection of MOC of Spiral Wound metallic Gasket winding material?
Answer: -
The selection of material of construction for Gasket winding depends upon: -
- The corrosive nature and concentration of fluid being carried.
- The operating temperature of the fluid.
- The relative cost of alternate winding material.
12. What are the most common materials used for spiral wound metallic gasket winding?
Answer: -
The most commonly used material for spiral wound metallic gasket winding is: -
- Austenitic stainless steel 304 with asbestos filler.
- Austenitic stainless steel 316 with asbestos filler.
- Austenitic stainless steel 321 with asbestos filler.
13. Which material is used as filler material for spiral wound gasket in case of high temperature services?
Answer: -
For very high temperature services, graphite filler is used.
14. What is centering ring in connection to spiral wound gasket?
Answer: -
Spiral wound gaskets are provided with carbon steel external ring called centering ring.
15. What will be the AARH finish on flange face for using spiral wound gasket?
Answer: -
125-250 AARH finish.
16. On which type of flanges the use of spiral wound gasket are restricted?
Answer: -
rating spiral wound gasket on flanges other#ASME B16.5 does not recommend the use of 150 than welding neck and lapped joint type.
17. Up to what temperature limits the low strength carbon steel bolts should not be used for flanged joints?
Answer: -
C.°C or below - 28°Flanged joints using low strength carbon steel shall not be used above 200
17. How the pipe fittings are classified based on end connections?
Answer: -
Pipe fittings are classified based on end connection as: -
- Socket weld fittings.
- Screwed end fittings.
- Beveled end or Butt weld fittings.
- Spigot socket fittings.
- Buttress end fittings.
18. Up to what temperature the carbon steel materials shall be used?
Answer: -
Carbon steel materials shall be used for temperature up to 425C°
19. Which material is used for temperature above 426C°?
Answer: -
Alloy steel materials shall be used for temperature above 426 C°
20. Which type of material is used for corrosive fluid?
Answer: -
Stainless steel materials shall be used for corrosive fluid.
21. Which type of piping materials are used for drinking water, instrument air etc?
Answer: -
Galvanized steel materials shall be used for drinking water, instrument air and NI lines (LP).
22. What is the difference between Pipe and Tube?
Answer: -
Pipe is identified by NB and thickness is defined by Schedule whereas Tube is identified by OD & its thickness as BWG (Brimingham wire gauge or 1/100 inch).
23. From which size onwards NB of pipe is equal to OD of Pipe?
Answer: -
From the size 14” and onwards NB = OD of pipe.
24. What should be the radius of long radius elbow?
Answer:
1.5D (Where “D” is the diameter of the pipe.)
25. What should be the radius of short radius elbow?
Answer:-
1D(Where “D” is the diameter of the pipe.)
26. What is the basis of using of short radius & long radius elbow?
Answer:-
Long radius elbow are used for small pressure drop whereas short radius elbow are used for high pressure drops. For catalyst flows vary long radius elbows are used.
27. Normally where do we use the following?
(1) Eccentric reducers. (2) Concentric reducers.
Answer:
- Eccentric reducers = Pump suction to avoid Cavitation, To maintain elevation (BOP) in rack.
- Concentric reducers = Pump discharge, vertical pipeline etc.
28. Concentric reducer is used in pump suction. (Yes / No). Explain.
Answer:
No. Air pockets may form if concentric reducer is used at pump suction, which results in cavitation
and cause damage to Pump. To avoid this problem, Eccentric Reducer with flat side up (FSU) is
used in Pump Suction.
29. Where the ERW spiral & longitudinal pipes are used?
Answer: -
Use depends upon the availability of pipes. Nothing functional difference.
30. Where the ERW & Seamless pipes are used?
Answer: -
Above 18” ERW pipes are used. Below 18” seamless pipes are used. Seamless pipes can sustain
higher temperature & pressure.
31. What is the main use of ASTM A53 & A106 Gr.B pipes?
Answer: -
ASTM A53 pipes are mainly used for utility services whereas A106 Gr. B pipes are used for high
Pressure & high temperature services.
32. From which side of pipe will you take a branch connection?
Answer:-
When fluid is Gas, Air or Steam and Cryogenic Service – Topside.
When Fluid is Liquid – Bottom Side.
33. Why don’t we take a branch for Cryogenic Service from bottom side though the fluid is in liquid state?
Answer: -
There is the chance of ice formation during normal operation and since ice flows from the bottom of the pipe it will block the branch pipe connection.
33. Why do we provide High Point Vent (HPV) and Low Point Drain (LPD) in piping?
Answer:
HPV – For removing Air during Hydro-test.
LPD – For draining water after conducting Hydro-test.
34. What do you mean by Jacketed Piping?
Answer: -
Piping which is recognized as providing the most uniform application of heat to the process, as well
as maintaining the most uniform processing temperatures where steam tracing is not capable of
maintaining the temperature of fluid constant. Usually used for molten sulphur, Polymers service.
35. What is the minimum distance to be maintained between two welds in a pipe?
Answer: -
The thumb rule is that the minimum distance between adjacent butt welds is 1D. If not, it is never
closer than 1-1/2". This is supposedly to prevent the overlap of HAZs. Minimum spacing of
circumferential welds between centerlines shall not be less than 4 times the pipe wall thickness or
25 mm whichever is greater.
36. What do you mean by IBR and which lines comes under IBR purview?
Answer: -
IBR: Indian Boiler Regulation Act.
Steam lines with conditions listed bellow comes under IBR purview : –
- Lines for which design pressure is 3.5 kg/sq. cm and above.
- Line size above 10” having design pressure 1.0 kg/sq. cm and above.
- Boiler feed water lines to steam generator, condensate lines to steam generator and flash drum.
37. What are Weldolet and Sockolet? And where they are used?
Answer:-
Weldolet and Sockolet are basically self-reinforced fittings.
Weldolet is used for Butt weld branch connection where standard tee is not available due to size
restrictions and the piping is of critical / high-pressure service. Sockolet is used for socket welding
branch connection, which require reinforcing pad.
38. What is the MOC for Superheated high pressure Steam Lines?
Answer:-
A 335 Gr. P I / P 11, Composition: Cr. – ½ Mo (P1) / 1¼ Cr. – ½ Mo (P11)
39. What is the normal upstream and downstream straight length of orifice flow meter?
Answer: -
Upstream - 15D Downstream - 5D
Friday 18 November 2016
Tuesday 15 November 2016
Piping Interview Questions related to Materials: -
Questions related to Materials: -
1. Q:-What is the ASTM code for the following?
- Pipes :-
- Carbon Steel II. Alloy Steel III. Stainless Steel IV. Nickel Steel.
- Tubes: -
- Carbon Steel II. Alloy Steel III. Stainless Steel IV. Nickel Steel.
- Wrought Iron Fittings: -
- Carbon Steel II. Alloy Steel III. Stainless Steel IV. Nickel Steel.
- Forged Fittings: -
- Carbon Steel II. Alloy Steel III. Stainless Steel IV. Nickel Steel.
- Cast Fittings: -
- Carbon Steel II. Alloy Steel III. Stainless Steel IV. Nickel Steel.
- Plates: -
- Carbon Steel II. Alloy Steel III. Stainless Steel IV. Nickel Steel.
Answer: -
- Pipes:-
- Carbon Steel : - ASTM A53 Gr. A/B, ASTM A106 Gr. A/B/C, ASTM A333 Gr.1/Gr.6
- Alloy Steel :- ASTM A335 Gr.P1/P2/P5/P7/P9/P11/P12/P22.
III. Stainless Steel :- ASTM A312TP304/TP304L/TP304H/TP308/TP310/TP316/TP316L/
TP316H/TP317/TP321/TP321H/TP347/TP347H/TP348/TP348H.
- Nickel Steel :- ASTM A333Gr.3/ Gr.8.
- Tubes:-
- Carbon Steel :- ASTM A178/179/192, ASTM A334 Gr.1/6.
- Alloy Steel :- ASTM A161T1, ASTM A213T1/T2/T5/T7/T9/T11/T12/T22.
III. Stainless Steel :- ASTM A213 TP304/TP304L/TP304H/TP310/TP316/TP316L/TP316H/
TP317/TP321/TP321H/TP347/TP347H/TP348/TP348H,
ASTM A608 HK40.
- Nickel Steel :- ASTM A334Gr.3/Gr.8
- Wrought Iron fittings :-
- Carbon Steel :- ASTM A234Gr.WPA/B, ASTM A420 Gr.WPL6.
- Alloy Steel :- ASTM A234 WP1/WP5/WP7/WP9/WP11/WP12/WP22.
III. Stainless Steel :- ASTM A403 WP304/WP304L/WP304H/WP309/WP310/WP316/
WP316L/WP316H/ WP317/WP321/WP321H/WP347/WP347H/
WP348.
- Nickel Steel :- ASTM A420WPL6/WPL8.
- Forged Fittings : -
- Carbon Steel :- ASTM A181. ASTM A105, ASTM A350 LF1/2.
- Alloy Steel :- ASTM A182F1/F2/F5/F7/F9/F11/F12/F22.
III. Stainless Steel :-
F321H/F347/F347H/F348.
- Nickel Steel :- ASTM A350 LF3, ASTM A522.
- Cast Fittings: -
- Carbon Steel :- ASTM A216, ASTM A352 LCB/C.
- Alloy Steel :- ASTM A217 WC1/WC6/WC9/C5/C12.
III. Stainless Steel :- ASTM A217 CA15, ASTM A296 CA15, ASTM A351 CF8/CF3/CH20/ CK20/CF 8M/CF 3M/CF 8C/HK40.
- Nickel Steel :- ASTM A352LC3.
- Plates: -
- Carbon Steel :- ASTM A285, ASTM A515, ASTM A516.
- Alloy Steel :- ASTM A387 Gr.2/Gr.5/Gr.7/Gr.9/Gr.11/Gr.12/Gr.22.
III. Stainless Steel :- ASTM A240 TP410/TP405/TP430/TP304/TP304L/TP309/TP310S/
TP316/TP316L/TP317/TP321/TP347/TP348
- Nickel Steel :- ASTM A203 Gr.D/Gr.E, ASTM A353.
2. Q:-What is the basic difference between Pipe specification A106 Gr.A / Gr.B/ Gr.C.?
Answer: -
Difference is due to the Carbon content.
% of carbon content in : -
- ASTM A106 Gr. A – 0.25 %
- ASTM A106 Gr. B – 0.30 %
II ASTM A106 Gr. C – 0.35 %.
3. Q:-What is the difference between pipe specification ASTM A312 TP 304 & ASTM A312 TP304L, ASTM A312 TP 316 & ASTM A312 TP 316L?
Answer: -
Difference is due to the Carbon content. The Letter “L” denotes lower percentage of carbon.
% of carbon content in : -
- ASTM A312 TP 304 - 0.08 %
- ASTM A312 TP 304L- 0.035%
III. ASTM A312 TP 316 - 0.08 %
- ASTM A312 TP 316L- 0.035%
Friday 4 November 2016
Thursday 8 September 2016
Q:-For what thickness will this Procedure be qualified if the required tests are successfully passed?
a. Unlimited
b. 1/8 to 2T inches
c. 1/8 to unlimited
d. Both a and b
e. Both b and c
b. 1/8 to 2T inches
c. 1/8 to unlimited
d. Both a and b
e. Both b and c
Friday 2 September 2016
Saturday 27 August 2016
Q:- Which of the following mechanical properties of a weld in carbon manganese steel is most affected, if the heat input per unit length of weld is excessively high:
a) Elongation
b) Tensile strength
c) Hardness
d) Toughness (impact value
b) Tensile strength
c) Hardness
d) Toughness (impact value
Subscribe to:
Posts (Atom)